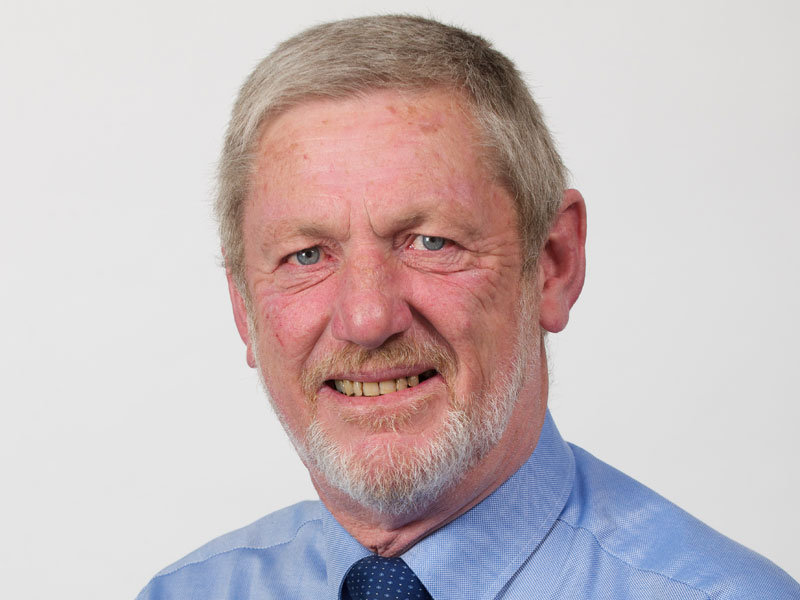
Author: Steve Hale, Technical & Business Development manager, Condair plc
The importance of humidity control in textile processing
In our everyday lives the humidity of the air around us very rarely merits discussion unless we are relaxing in a sauna or holidaying near the equator. However, there are not many occasions where humidity is more of an issue than during the processing of textiles. Get it wrong and it can stop production, damage machinery and harm staff. Get it right and you can maximise product weights, improve quality and increase machine speeds.
Air humidity is measured as “relative humidity”. It is defined as the amount of water in a sample of air compared to the maximum amount of water the air can hold at the same specific temperature. It’s expressed in a form of 0 to 100%.
Cold air can hold less moisture than warm air therefore the humidity of air is “relative” to its temperature. For example, a sample of air at 10oC can hold less moisture than the same sample of air at 20oC. Even with the same amount of water present in both samples, the warmer sample has a lower relative humidity as it can potentially hold more moisture than the cold air sample.
...change in moisture content has a direct impact on the properties of textiles, such as tensile strength, elasticity, fibre diameter and friction.
This means that even in humid climates, the indoor air humidity can be low when cool humid air from outside enters a textile production facility and its temperature rises. An increase in temperature of 20oC can lead to a typical drop in humidity of around 60%rH (relative humidity). This means that humid air entering a building at 80%rH would decrease to just 20%rH when heated. This can cause major problems for textile production.
Why humidify?
All textiles are hygroscopic. That is, they absorb or release moisture depending on the relative humidity of the surrounding air. If the atmosphere is drier than the textile’s equilibrium relative humidity then the textile will give up its moisture to the air. If the air is very humid then the textile’s moisture content will increase. This moisture loss and gain occurs at every stage from the initial processing of the fibres through to final garment manufacturing, distribution and use by the consumer.
This change in moisture content has a direct impact on the properties of textiles, such as tensile strength, elasticity, fibre diameter and friction. A drop in the equilibrium relative humidity of a textile may cause it to be weaker, thinner, less elastic and therefore more brittle. It will also have more imperfections. By maintaining the air humidity whilst processing the fibres, this loss in moisture to the atmosphere is minimised.
Moisture loss during processing cannot be totally eliminated as the act of processing will increase the temperature of the material, which will cause it to become drier. However, by increasing the humidity of the air surrounding the textile directly after processing, the material experiences “regain”. Moisture is reabsorbed by the textile, thus improving the quality and performance of the fabric.
This regain also has a direct impact on the weight of the textile. As textile yarns are sold by weight, if a drop in humidity leads to a 4% reduction in weight, this will require 4% more fibre to be included in the sale product. For a mill manufacturing 80 tonnes of textile per day, this can lead to a loss of 3,200kg of product per day due to incorrect humidity control.
Static
The occurrence of static can be a major problem when processing textiles and it is directly related to levels of relative humidity. The electrical sensitivity that determines whether static electrification will occur is dependent on the moisture content of the air and fibres. As the fibres lose moisture, they increase their electrical resistance. This means they can no longer easily dissipate the electrical charge which is generated by the frictional contact with the machinery.
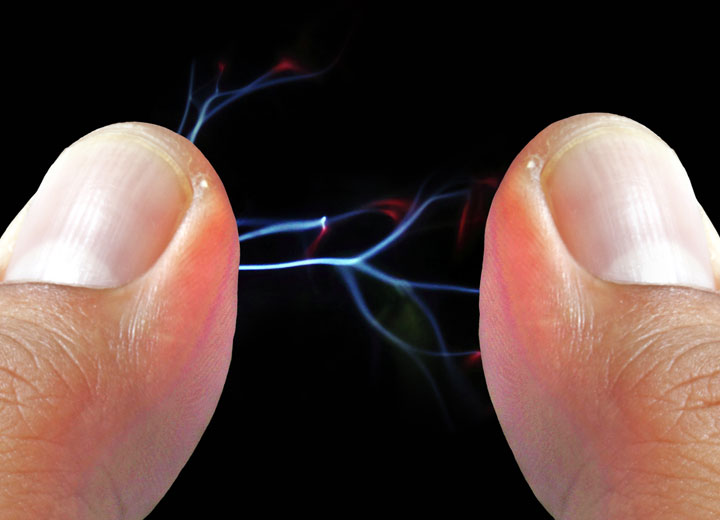
In a production facility with a low humidity, static discharges can jump up to 4-5 inches...
In a textile production facility with a low humidity, static discharges can jump up to 4-5 inches and, although they have a low current, can build up to several hundred thousand volts. This presents a danger to staff working with the machines as it is not only very uncomfortable if they are shocked, but it can cause a person to jump and fall, which presents extreme risks when working near to textile machinery. The static discharge can also present a direct health risk to people with weak hearts or pace makers fitted.
As well as the physical danger to staff, static electrical build-up will cause materials to stick together and be less manageable. This in turn will slow machinery, directly effecting production schedules. Also, as most machines are now microprocessor controlled, an uncontrolled electrical discharge in the wrong place can damage the electronics of the unit resulting in expensive repair bills and significant downtime.
By maintaining humidity at around 50%rH, static build-up is eliminated and all these associated problems are avoided.
Another advantage of maintaining the correct humidity in processing facilities is that it reduces airborne particles. A higher humidity encourages airborne lint, dust and fly to precipitate out of the atmosphere. Also, if a cold water humidification system is used, the evaporation of the water into the air causes an adiabatic cooling effect that can reduce ambient temperatures by between 2-6oC. These additional benefits of using humidifiers create a healthier, less polluted, more pleasant atmosphere for workers and a more productive workforce.
Humidity levels
So what is the ideal humidity? Well this depends on the type of textile and the process being undertaken. Natural fibres are far more susceptible to moisture than manmade, in terms of performance. However manmade textiles suffer more with static charge build up.
Cotton and linen have to be processed at very high levels, around 70-80%RH, because they are very brittle. By humidifying each process, from the combing of the raw material, through carding, twisting, spinning and weaving, the manufacturer can ensure that the product remains flexible and is prevented from breaking. This is important since the longer the fibre, the finer the thread that can be spun from it.
Wool is similarly susceptible to dry air, although a little more forgiving, requiring humidity levels of around 65%RH. Man-made fibres also require the correct, albeit lower, level of humidity since below 45%RH they are prone to a build-up of static electricity. Silk should be processed at between 65-70%RH, although artificial silk spinning requires a higher level of 85%RH.
The most effective way to humidify a textile plant is to use a compressed air and water spray system, such as the JetSpray...
How to humidify
The most effective way to humidify a textile plant is to use a compressed air and water spray system, such as the JetSpray from Condair. Rows of precision engineered nozzles are mounted in the roof space and combine compressed air and water, releasing a fine mist. This mist resembles pressurised steam and contains droplets of just 7.5µm, which rapidly evaporate to raise the humidity to the required level.
This type of spray system is easy to install and provides very reliable and hygienic humidity control. It is also flexible and easy to locate, which is convenient in situations where machinery and processes can periodically be relocated. The capacity of the humidification system can be increased in size or modified simply by adding more nozzles. On a quality system, an individual control panel should be able to accommodate rows of nozzles releasing a total of up to 600 litres of water per hour. This could typically humidify a textile manufacturing area of around 100,000m3.
If a particular process or area requires humidity control, rather than humidifying a complete room, localised spray systems are available. They can be mounted on a piece of textile machinery or be free standing and can either spray directly on to a process or create the desired humidity in the immediate vicinity. This saves money by eliminating the need to control the atmosphere in a much larger area requiring many spray nozzles and long runs of pipe.
Hygiene
Hygiene is of paramount importance when releasing water into an atmosphere as any viruses or bacteria in the water could potentially be inhaled by people in the vicinity. Modern humidification systems incorporate a variety of hygiene features but the most effective type should combine both flush cycles and a form of silver ion dosing. The flush cycles will ensure that water cannot stagnate in the pipes and allow bacteria to form. Any cold water humidification system should typically auto-flush at least every 24 hours.
Silver ion dosing is a relatively new development in hygiene control in humidifiers. As silver is effective against over 650 types of bacteria and virus, it provides added reassurance by eliminating any organisms in the water before they enter the system. Silver also has a residual effect throughout the pipework. In the past humidifiers typically used to incorporate UV sterilisation but this can potentially allow viruses to enter the system “shadowed” by particles in the water, or allowed in by UV bulbs that have dulled with age.
Regular servicing is also an important aspect of hygienic humidification. No matter what hygiene features a system has, inspections should be carried out by a competent individual from time to time to ensure optimum and hygienic performance. Spray systems, such as the JetSpray from Condair, incorporate self-cleaning nozzles that can reduce maintenance to just an annual check.
Good advice
The most important thing to remember when considering humidity control is to get good advice from an expert with experience in the textile industry. There are many different issues involved with humidification of textile plants and as the issues described above demonstrate, getting it wrong can be an expensive mistake.